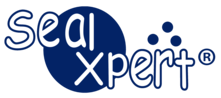
Types of Breakdown of Corrosion Protection Coatings
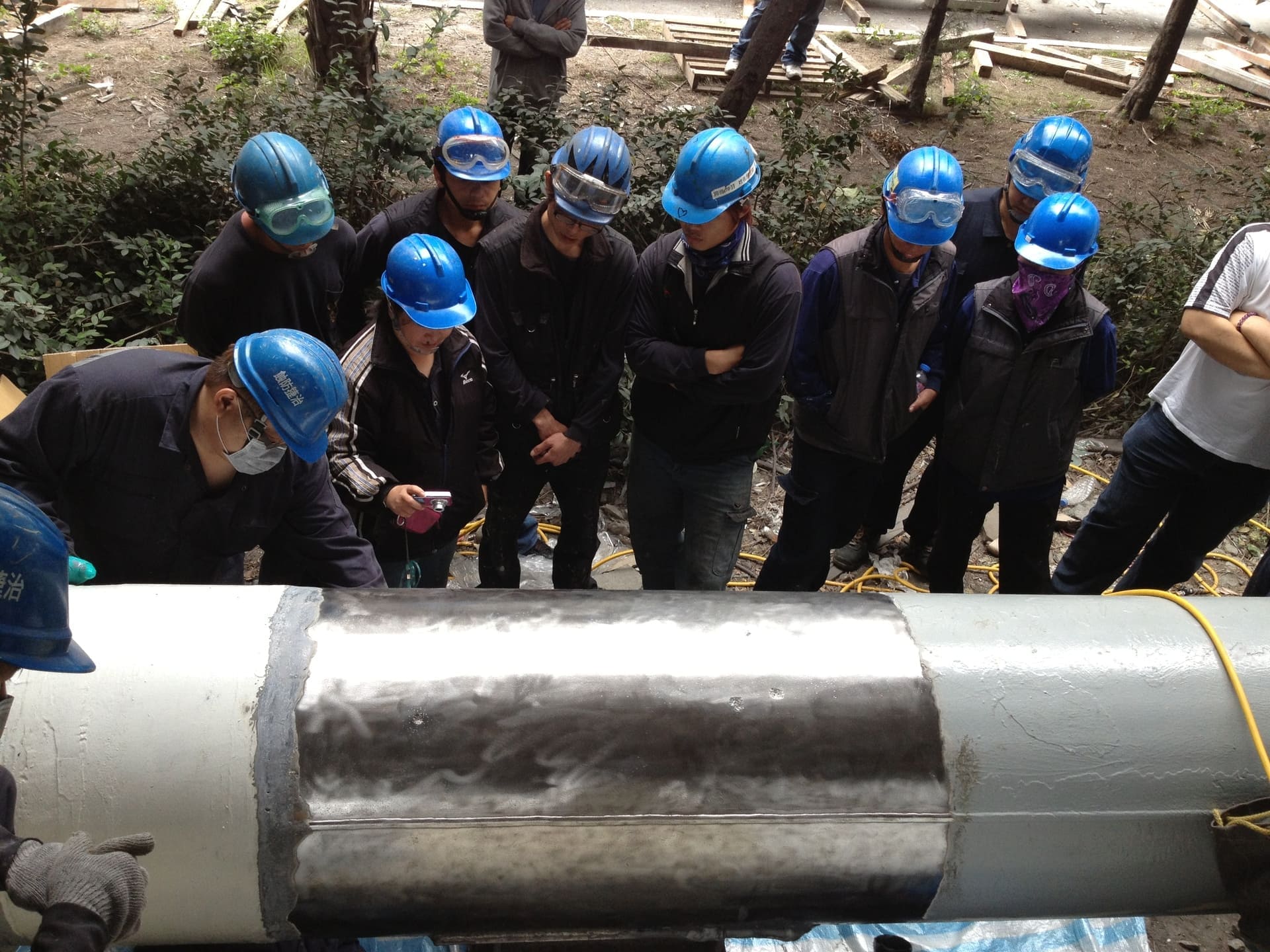
Introduction
Anti-corrosion coating breakdown is covered here from a physical viewpoint.
BLISTERING VIA OSMOSIS
Blistering is usually caused by the presence of ionic contamination or water soluble species at the interface between the anti-corrosion coating and the steel. Water is drawn from the environment through the anti-corrosion coating from an area of low ionic concentration to an area of high ionic concentration by osmosis. The anti-corrosion coating domes upwards as a result of the pressure difference.
BLISTERING VIA ELECTRO OSMOSIS
Osmotic blisters are usually small and relatively closely spaced. Larger blisters are the result of electro osmosis. When a normal blister grows so that it encompasses a pore in the anti-corrosion coating, electro osmotic blistering can take place. The difference in potential between the anodic site and the local cathodic site that occurs beneath the blister drives ions into the blister. These then result in further growth of the blister via the mechanism. An actively corroding site or an external sacrificial anode would provide the same driving force for blistering. Osmosis and electro osmosis tend to occur early in the lifetime of an anti-corrosion coating while it retains a degree of plasticity.
RUST JACKING
Rust jacking or rust leverage is the predominant mechanism of anti-corrosion coating failure during the late stages of the service life of the anti-corrosion coating. It occurs at defects in the anti-corrosion coating, cut edges, welds and at sites of mechanical damage. It is a result of the change in volume that occurs between iron in the steel and iron in the corroded condition. Typically, a volume increase of between eight and 12 times is involved when iron becomes rust. This volume change occurs beneath the anti-corrosion coating and mechanically levers it from the surface. Good mechanical strength in the anti-corrosion coating and a good mechanical key to the substrate both help to resist this occurrence.
CALCAREOUS DEPOSIT JACKING
Calcareous deposit jacking is similar to rust jacking in that the anti-corrosion coating is levered from the surface mechanically by a deposit growing beneath it. In this case, the white calcareous deposits grow at the interface of the steel and anti-corrosion coating as a result of electrochemical polarization by the cathodic protection system. Hydroxyl ions are generated at the cathodic site beneath the anti-corrosion coating. These ions change the pH of the environment, which in turn changes the solubility of components of the sea water and cause precipitation to take place in this area. Dissolved carbon dioxide can also diffuse into the gap under the anti-corrosion coating and react with the hydroxyl ions, giving rise to chalky deposits.
Calcareous deposit jacking and rust jacking usually occur together (sometimes in alternating layers) due to the cyclic conditions found in ballast tanks. It should be noted that the calcareous deposits which grow, help to protect the steel from further corrosion by the formation of a barrier layer on the steel. This is particularly of benefit in the ballast tanks of bulk carriers which suffer from impact damage from grabs, etc., on the opposite side of the plate in the cargo holds. The paint in the ballast tanks can crack or become detached and the calcareous deposits assist in the prevention of rapid corrosion at these areas until repairs to the anti-corrosion coating can be carried out.