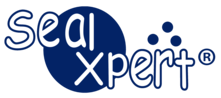
REPAIR PUTTY
SEALXPERT PL105 RUBBER REPAIR PUTTY
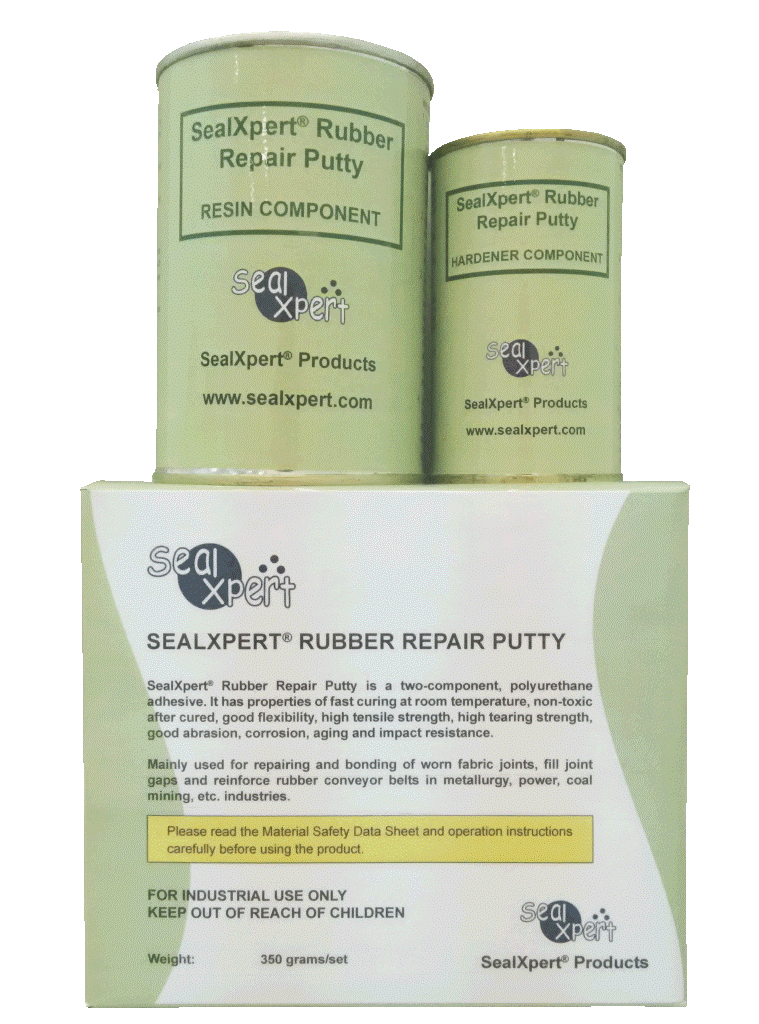
SealXpert PL105 Rubber Repair Putty is a two component neoprene and polyurethane-based, ambient-temperature curing rubber putty. It has properties of high initial bonding strength, good toughness, curing at room temperature. After curing, the repair putty has high flexibility and excellent chemical resistance against acids and alkalis. SealXpert PL105 Rubber Repair Putty designed to bond joint of fabric enforced multilayer rubber conveyor belt in various industries and to bond rubber, leather, metal and ceramic to each other.
Typical applications of SealXpert PL105 Rubber Repair Putty: impeller coating recovery, rubber hopper repair in mining rucks, pulley recovery, repair of all types of coating of natural or synthetic rubber; protection of pieces and equipment exposed to acid environments, recovery of rubber lifters in agglomerate drums, etc.
SealXpert PL105 Rubber Repair Putty is sensitive to moisture and is prone to foam, which has negative effect on quality and strength. So it is recommended to avoid storing or using the repair putty under conditions of low temperature (under 15°C) and moist environment (above 90% humidity).
RUBBER CONVEYOR BELTS WORN-OUT & THROUGH-HOLE REPAIRS
Surface Preparation:
- For thin rubber thickness (3mm or less), the damaged zone must be roughen with an power tool wire brush at low rotation speed (750rpm to 900rpm) on and around the damaged zone. For thicker rubber thickness greater than 3mm, a 45° bevel must be cut around the edges of the damage area so as to create a trapezium shape around the damaged area. Roughen with an power tool wire brush at low rotation speed (750rpm to 900rpm) on and around the damaged zone. In the event of passing rips or damage, perform the same procedure including also the lower surface.
- Before applying the repair putty, ensure that the application surface is always be dry, clean, and free of impurities. Clean the surface thoroughly with an abrasive pad and solvent-based contact cleaner & degreaser. If the chosen area is wet, it must be dried with a hot air gun. If humidity is high, the scraping process will suffice to remove the first layer of rubber that is wet.
- For though hole rubber conveyor belt repair, adhere a layer of non-stick PVC film or several layers of masking tape on the bottom side of conveyor belt, to prevent mixture from running off of repair putty. Secure the PVC film or masking tape with staples in the lower part of the damage.
- SealXpert PL105 Rubber Repair Putty consists of resin and activator each separately packed. The resin container is slack filled to allow the addition of activator to be mixed with resin. Pour the hardener component of SealXpert PL105 Rubber Repair Putty to the resin container in accordance to mixing ratio and stir vigorously for 2 minutes. Ensure the repair putty is mixed evenly.
- The mixing process is complete when the product is free from streaks or other variances. It is critical to mix the repair putty thoroughly and in proper ratio to achieve the performance of the material. Failure to thoroughly mix the material will cause soft spots or overall failure of the product. Whenever possible, the complete container should be mixed at one time. If the material is to be mixed in separate batches, the user must be careful to adhere to the mixing ratios specified on the product label.
- Pour half the mixture onto the treated worn rubber surface. Spread the mixture evenly over the worn rubber surface with a scraper.
- Allow the rubber repair putty to cure for approximately 10 minutes and remove the PVC film or masking tape.
- Allow the rubber repair putty to cure for minimum of 2 to 3 hours before commence operation.
- The repair job is completed.