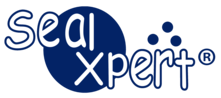
Important Aspects of Surface Coating for Anti-Corrosion
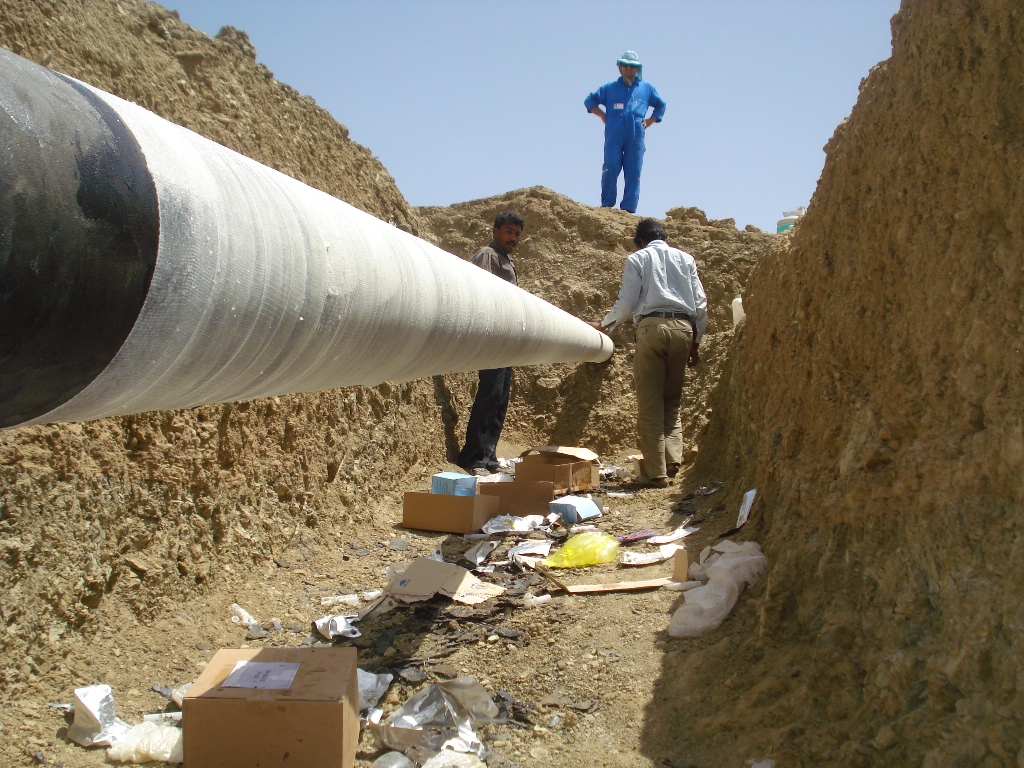
Introduction
Corrosion issues are clearly of economic costs and corrosion can lead to structural failures that have dramatic consequences for humans and the surrounding environment. Reports on the corrosion failures of metal structure, bridges, aircrafts, automobiles, buildings, and gas pipelines are not unusual. Both organic and inorganic coatings have been widely applied for the protection of metals against corrosion. In many areas of coatings technology the fight against corrosion has made significant progress in recent years. Despite significant improvements in corrosion coating technologies problems will continue to persist in the long term protection of metal from aggressive environments.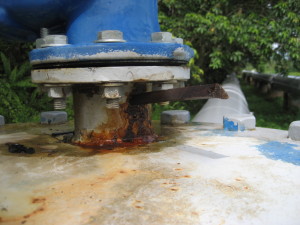
1. Coating additives
Paint additives and coating additives include a wide range of materials added to polymer resins, paints and coatings and other substances to modify specific properties. They include insulating paint additives, powder coating additives, catalysts, wetting agents, levellers, clarifier, coupling agents, deflocculates, thinners, thickeners, anti-caking agents and other chemicals. Paint Additives and Coating Additives are available in many different forms. A wide range of paint additives, coating additives, insulating paint additives and powder coating additives made from the finest quality raw materials. These products are effective in providing water resistance, corrosion resistance, heat resistance and abrasion resistance. Our paints and coatings additives are safe and environment friendly.

- Two components mixing system
- Quick Drying at room temperature
- Self-Priming (No need to apply primer)
- Tough & Scratch proof
- Fire Resistance – BS-163
- Excellent resistance to U.V. Radiation
- Resistance to Acids, Alkalies & saline atmosphere.
- Stable up to 200°C
- Easy to apply by Brush
- No skill manpower requirement.
- Quick & Convenient
- Considerable reduction in painting time.
- Applicable on Ferrous & Non-ferrous metals.
- Saves cost as compared to conventional protective paints
- Reduces the delivery period due to fast & short painting process.
- Saves Manpower & Time.
- Equipment Structural Steel
- Industrial Valves, Motors & Pumps
- Control Panels, Transformers
- Pipe Lines, Storage Tanks
- MS Structures, Chemical Plants/
- Refineries/Thermal Power Complexes
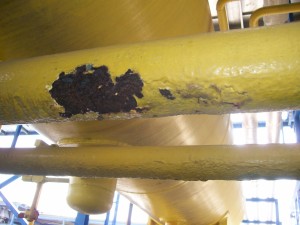
- Form: Liquid
- Odour : Non
- pH : Neutral
- Density : 1.01 (+/- 0.02) at 27°C
- Viscosity : 24 sec. ( B-4 Cup ) at 270°C
- Touch Dry 60 minutes at 30°C
- Re-coating 90 minutes
- Hard Dry 24 hours
- Coverage 0.5m2 per litre per coat (Flat Area)
- 2mm/ per coat – Brush Application
- Application Method Conventional Brush Technique
- Surface Requirement Free from dust, rust, oil, grease & any other Foreign Deposits.
- Flexibility (Conical Mandrel) 4mm: No Film Crack
- Impact ( 60 Kg/Cm2): No Film Crack
- Adhesion Passes Gt O
- Scratch Resistance: 4.5 kg
- Thermal Stability 230°C ( Continuous)
- Immersion in cold water for 7 days : No Effect Observed
- Immersion in Boiling water for 24 hours : No Effect Observed
- Immersion in Lubricating Oil for 7 days : No Effect Observed
- Immersion in Vegetable Oil for 7 Days : No Effect Observed
- Immersion in Kerosene : No Effect Observed
- Salt Spray Resistance 1500 hours : No corrosion
- Exposure to mix. Of 20% HCL & 18% H2So4: No Deterioration of film
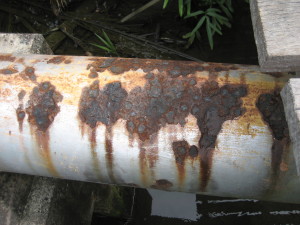