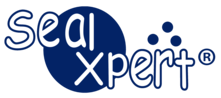
Corrosion Resistance through the Application of Anti-Corrosion Coatings
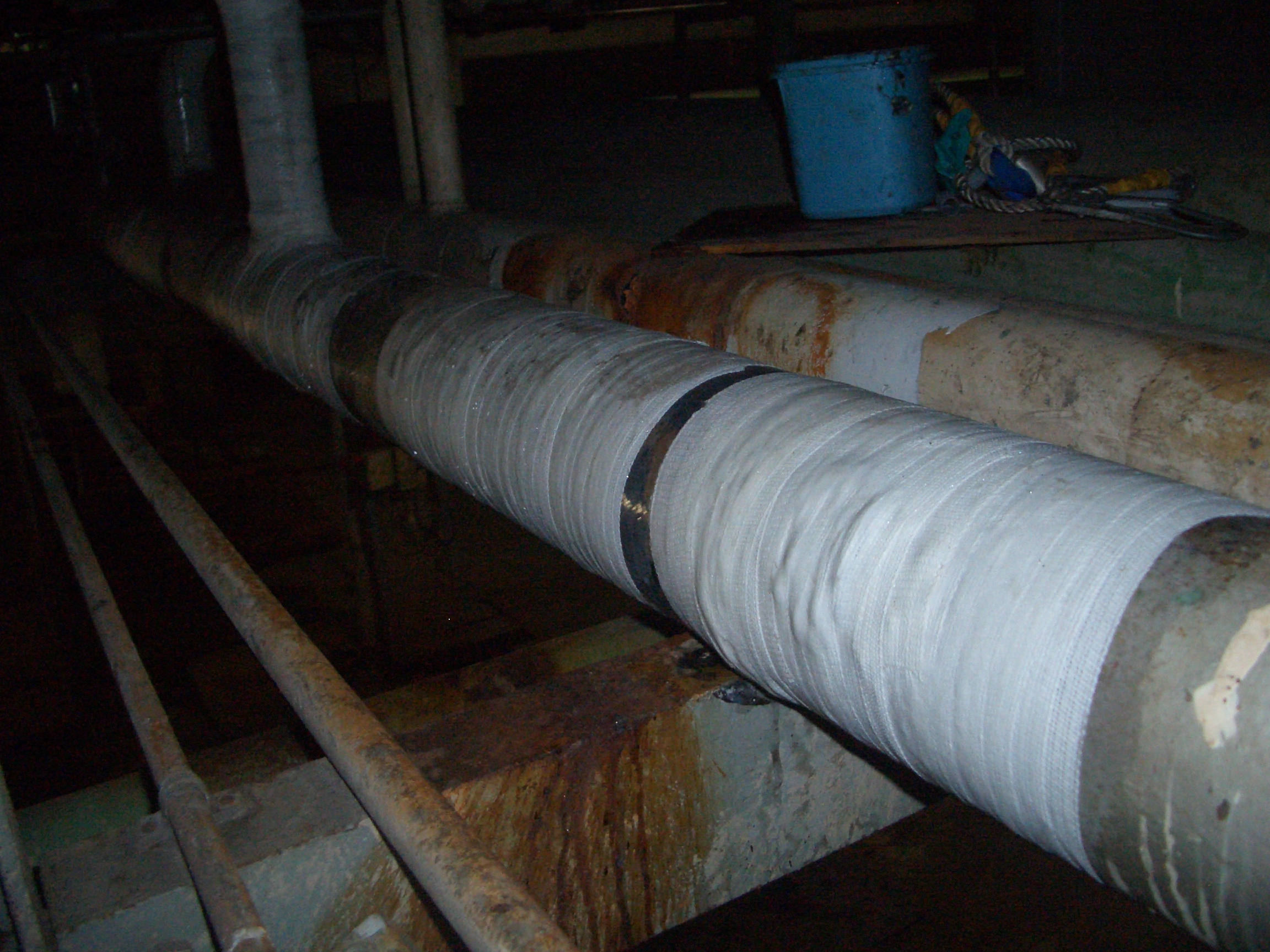
Introduction
Corrosion is the surface disintegration of metals within specific environment. There are basically three factors by which corrosion can be classified – nature of the corrodent, mechanism of corrosion, and appearance of the corroded metal. The classification is based on the surface morphology and it must be noted that the forms of corrosion are distinct in theory but practically, there are cases wherein the corrosion fits in more than one category. The corroded metals can be grouped into six forms of wet corrosion and these are:
- General corrosion, pitting corrosion, crevice corrosion;
- Galvanic corrosion, erosion-corrosion, cavitation erosion;
- Fretting corrosion, intergranular corrosion;
- Exfoliation, dealloying, dezincification;
- Environmentally assisted cracking, including stress cracking corrosion, corrosion fatigue;
- Hydrogen damage.
Anti-corrosion coatings: Mechanism
There so many mechanism of anti-corrosion coatings but generally, mechanism of coating can be differentiated into three, namely; barrier creation between substrate materials and environments, inhibition of the corrosion processes, and coating acting as sacrificial materials.
Corrosion prevention and control
Materials are protected from corrosion through a wide variety of methods. In some measures, corrosion is avoided by careful choice of material and design of system so that the opportunity for corrosion of a certain specific sort does not arise. In most cases, the occurrence of corrosion is prevented or suppressed by the modification of the environment, modification of the materials properties, application of protective coatings and, cathodic and anodic protection. However, it must be noted that the principles of corrosion prevention is based on modification of environments, electrochemical approaches, and corrosion resistant materials. The importance of coating cannot be emphasized because it encompasses all the corrosion control and prevention techniques such as cathodic protection (sacrificial), modification of environment (barrier effects and inhibition), and materials selection (development of corrosion resistant materials such as conducting polymers).
Coatings
Coating materials can be metallic, inorganic or organic. Relatively thin coatings of metallic and inorganic materials can provide a satisfactory barrier between metal and its environment. The chief function of such coating is to provide an effective barrier except for sacrificial coatings such as zinc.
Metal coatings are applied by electrode position, flame spraying, cladding, and hot dipping and vapour deposition but inorganics are applied or formed by spraying, diffusion, or chemical conversion. Spraying is usually followed by baking or firing at elevated temperature. Metal coatings usually exhibit some formability whereas the inorganics are brittle and in both cases a complete barrier must be provided. Porosity or other defects can result in accelerated localized attack on the basic metal because of galvanic effects.’
Organic coatings involve a relatively thin barrier between substrate material and the environment. Paints, varnishes, lacquers, and similar coatings doubtless protect more metal on a tonnage basis than any other method for combating corrosion. Aside from proper application, the three main factors to consider for organic coatings are listed in order of importance as surface preparation, type of primer or priming coat and the selection of topcoat or coats.
Surface preparation is considered as one of the topmost factors in coating industry. It is known that if the metal surface is not properly prepared, the paint may peel off because of poor bonding, If the primer does not have good adherence or is not compatible with the top coat, early failure occurs. If the first two factors are wrong, the system will fail regardless of the topcoat used. Poor paint performance is in most cases due to poor application and surface preparations. A tremendous variety of paints are available. Asphalt bituminous paints are often used on pipelines. Sometimes reinforcement wrapping is applied with the coating for reinforcement. Alkyds, glyptols, concrete, lead, iron oxide, phenolics, lithopones, titanium oxide paints and chlorinated rubber are just a few examples. Vinyl and epoxy paints have been widely adopted for corrosion application. There are many traditional techniques of coating, the techniques are thermal spraying, ion beam, immersion, welding, screen printing, dip-coating, electrogalvanising process, coating under vacuum, etc.
A typical example involved the use of cold reinforcement tape coating and wrapping system on new or reconditioned pipelines carrying oil, gas and water. Their main function is to provide long term corrosion protection from underground elements as well as mechanical protection. The total reinforcement tape system components consist of a primer applied directly to the pipe surface, an inner-wrap tape layer that provides a corrosion barrier and an outer-wrap tape layer that provides mechanical protection.
Conclusion
Militating against corrosion is necessary in the industry because the penalties of failures due to corrosion can be very costly including safety hazards. Material loss and component failures can be prevented with proper selection of coatings and materials in most manufacturing industries. Adequate knowledge of these processes is therefore inevitable. Anti-corrosive coatings produced new materials surfaces with numerous functional properties and unique features.