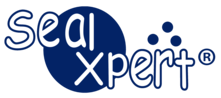
Application Techniques for Anti-corrosion Coatings
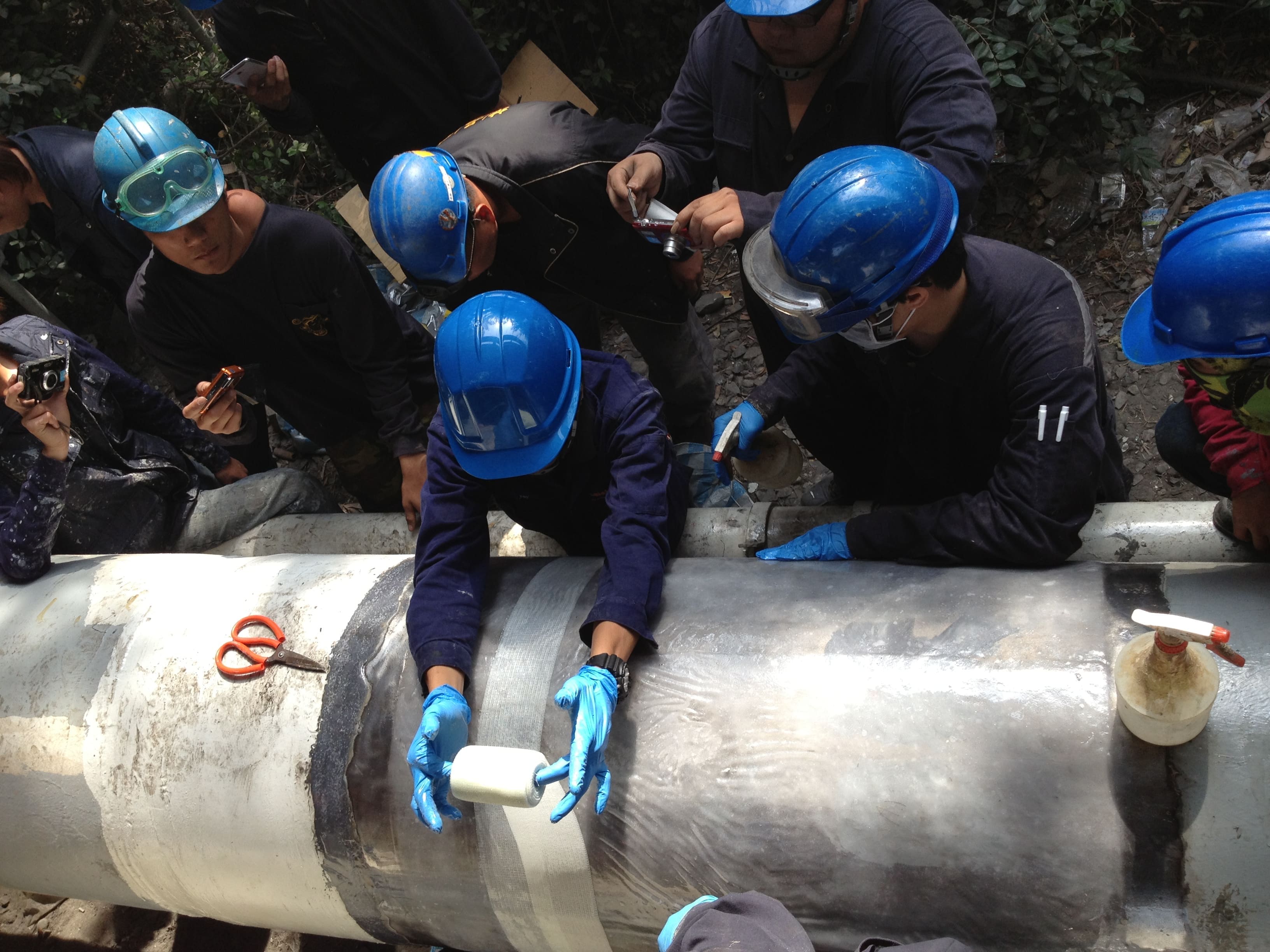
Introduction
The objective in applying anti-corrosion coatings is to provide a film which will give protection and/or decoration to the structure being applied. The variables which govern the success of any application and subsequent performance are:
• Surface preparation
• Film thickness of the paint system
• Methods of application
• Conditions during application
Surface Preparation
As detailed in the previous chapter, it is essential that a good standard of surface preparation is achieved, if the anti-corrosion coating is to perform successfully in service.
Film Thickness Measurement
An adequate film thickness is necessary for an anti-corrosion coating system to perform to expectations and provide good anti-corrosion protection lifetime, etc. Under thickness will result in premature failure. However, over application can also cause problems, such as solvent entrapment and subsequent loss of adhesion, cracking of the coating (including mud-cracking) or splitting of primer coats.
Ideally the anti-corrosion coating thickness should be that specified, allowing for practical application variations. The wet film thickness (WFT) of the anti-corrosion coating is measured and can be converted to a dry film thickness (DFT) following the coating manufacturer’s guidelines for that product. The wet film thickness measurement can serve as an aid in determining how much anti-corrosion coating should be applied to reach the specified DFT. The dry film/wet film ratio is based on percentage of solids by volume of the anti-corrosion coating being used. Coating manufacturer’s data sheets sometimes list solids by weight as well as solids by volume.
The basic formula using solids by volume is:
WFT = DFT (% solids by Volume)
The actual DFT specified will depend upon the type of paint being applied and the nature of the substrate surface. To determine whether an anti-corrosion coating thickness is acceptable, there are guidelines produced by the coatings manufacturers, such as the 80-20 and 90-10 rules. For example, the 90-10 rule means: no measurement may be below 90% of the DFT specified without repair being undertaken and not more than 10% of the measurements may be in the range 90-100% of the DFT specified without repair being undertaken. The figures will depend upon the type of anti-corrosion coating being applied and the area of the vessel being coated. Measurements of the dry film thickness are influenced by the profile of the substrate, particularly when abrasive blasting has been used. Thin films (of less than 25_m) cannot be measured accurately over blasted surfaces using commercially available paint thickness gauges. Measurements of DFT at edges and corners are not accurate due to the measurement techniques used by these gauges. Coating companies can advise on suitable methods for these circumstances.
Methods of anti-corrosion coatings application
The normal methods of application of anti-corrosion coatings are by:
• Brush
• Roller
• Conventional Air Spray
• Airless Spray
(1) Brush Application
Brush application is a relatively slow method and is generally used for the coating of small complicated or complex areas or where the need for ‘clean’ working with no overspray precludes the use of spray application. Brushes are also used for applying surface tolerant primers, where good penetration of rusty steel surfaces can be achieved with operator persistence. Brushes are a commonly used method for “touch up” of coatings during service.
It is important not to ‘over-brush’ the surface, as this will result in large variations in film thickness, which is the inherent problem with brush application. Care must also be taken when applying thermoplastic coatings over one another as the solvents in the wet top coat can dissolve the lower coating. Even and light brush strokes are required to avoid pick up of the previous coat, otherwise a very rough finish will result. It is generally not possible to achieve the required film thickness in the same number of coats as with spray paint application and multi-coat applications are necessary to give the specified film build.
Application by roller is faster than with a brush on large, flat surfaces, such as walkways and deck areas, but it is not so good for complex shapes. It is hard to control film thickness and high film build is generally attained by applying multiple coats. The correct choice of roller pile is dependent on the type of anti-corrosion coating and the roughness and irregularity of the surface being coated and is essential for a good finish. Rollers can be used for applying stripe coats under certain circumstances to areas such as rat holes and cut outs.
(3) Conventional Spray
This is a method commonly used for applying single component zinc silicates to large surfaces. The equipment is relatively simple and inexpensive and is usually confined to fairly low-viscosity coating. Coating under pressure and air are fed separately to the spray gun and mixed at the nozzle. The coating is atomized and air is mixed with these droplets forming a fine mist of paint which is carried by the air pressure to the work surface. It is essential to use the correct combination of air volume, air pressure and fluid flow to provide good atomization and a coating film which is free from defects. Poor control gives rise to overspray and rebound from the work surface defects in the coating.