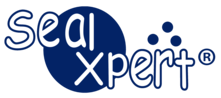
5 Steps to Repair an Active Pipe Leaks
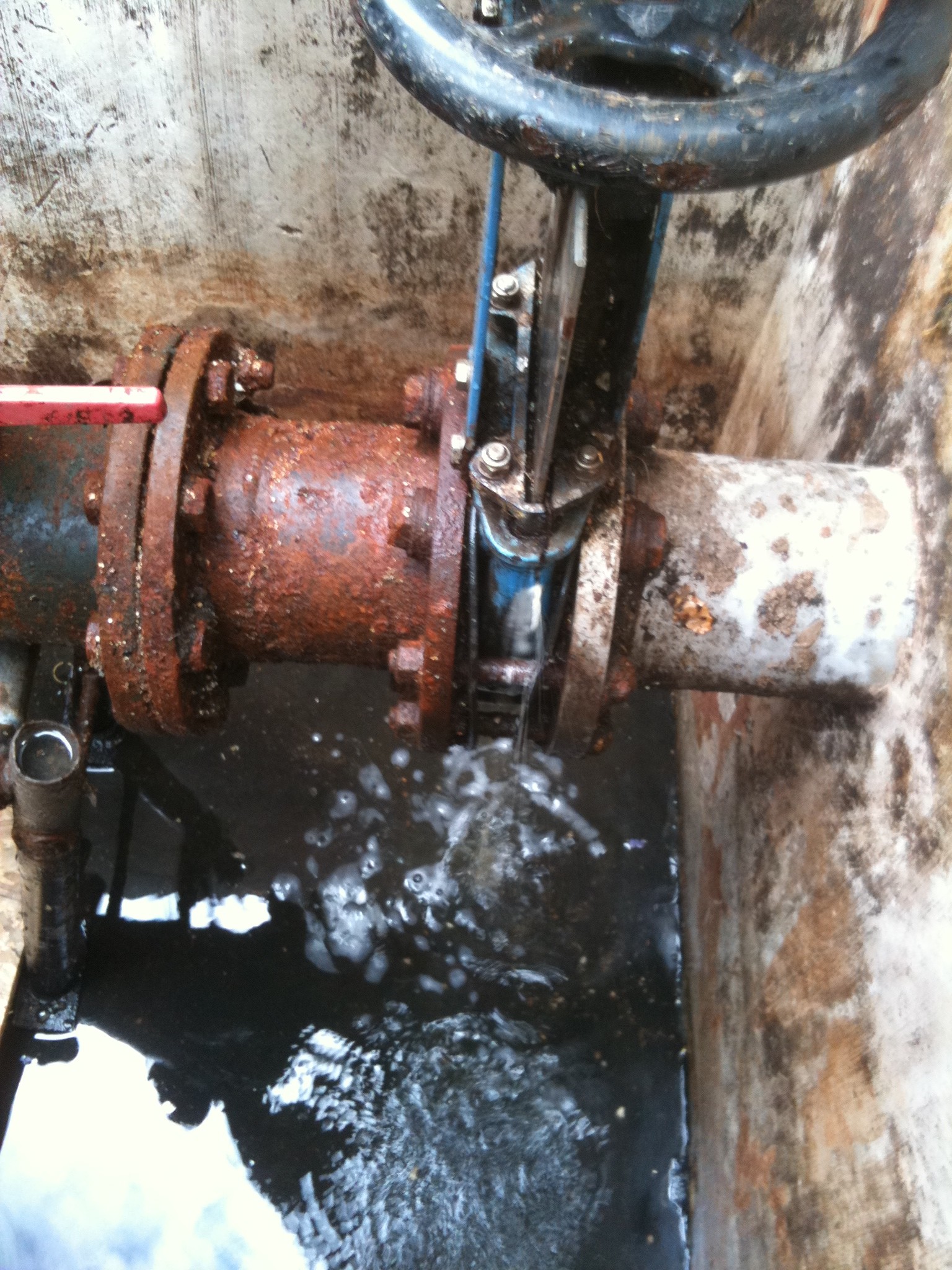
Introduction:
Pipe erosion happens routinely and complete wall loss of pipe or through-crevice flaws are a general occasion at various spots.
In the Oil & Gas and Offshore industry where burnable gases are accessible, it is imperative to modify these types of pipe leaks and pipe blemishes with cold curing repair. This is because hot works are more or less unsuitable.
Composite repair system using composite wrap must meet the fundamental essentials and perform at the typical level under convincing conditions. Different composite repair materials are open on the market today, such as repair putties, but there are few that have the testing and ability to perform at the increased temperatures which may require more experience.Gathering Pipeline Data & Information
While performing online pipe leak repairs, it is essential to follow in consent to ASME PCC2 and ISO 24817 rules and necessities. All data for the pipeline working weight, temperature, pipe size and pipe medium should be gathered and dissected.
Point by point Engineering Calculation and Application Method of Statement
A point by point building engineering calculation and report especially focused on the pipe leak must be made to choose the sum and sort of materials to be used. The system for application requires organizing a systematic repair system, which may be given and supported by the client.
Site study should be driven before work launch, so all perils are assessed and broken down into a threat assessment report. All Personnel Defensive Equipment should be worn and peril allaying/diminishing steps should be used to minimize or stay far from every pointless threat.
Surface Preparation of Affected Pipe Section
Before work starts, reliably endeavor to stop or decrease the pipeline pressure and temperature to the most extreme capacity. Starting surface preparation by using the grit blasting system – purify the influenced pipe surface to SA 2.5 standard when conceivable. At regions where grit blasting is unachievable, these ranges ought to be purified with fitting non-spark mechanical assemblies. The length of surface arranging should be in consent to the Engineering Calculation Report given. While performing surface arranging, the pipe surface should stay dry all through the session.
Set up the pipe surface roughness to around 60 to 80 microns. Use a surface roughness analyzer to insist that the masterminded surface harshness has been achieved.
Launch of Pipe Leak Repair Works
Pipe leak repair methodology should begin within 4 hours after the surface plan has been done. Before the beginning of pipe repair works, verify the leak region is checked thoroughly.
Utilize the latex gloves and take enough amount of SS106 Seal Stic underwater epoxy stick to cover the scope of the leak. Put the mixed Seal Stic onto a stainless steel sheet metal. Thereafter, set up a couple of packs of SealXpert stainless steel clip by cutting a fitting length of the steel clip.
Connect the cut-off length of stainless steel clip with portable fasteners. Wrap the connection with portable fasteners and PVC tape. Put the stainless steel backing against the SealXpert stainless steel clip while the Seal Stic confronts the pipe surface, far from the leak zone. Fix the portable fasteners of the SealXpert stainless steel clip and slide the couple of sets of fasteners to the leak zone. The SealXpert stainless steel clip should be arranged next to each other, securing both the core and edge of the leak zone. Continue to tighten the mobile fastener of the SealXpert stainless steel clip while ensuring that the Seal Stic is securing the opening of the leak.
Changing of Affected Pipe Section
At the point when the leak is caught, use SealXpert PS102 metal repair putty. Mix the hardener piece of PS102 metal repair putty into the resin dish and utilize the mixed repair putty over the prepared pipe region. The thickness of the cover should be in consent to the Engineering Calculation Report given. Grant the secured SealXpert PS102 repair putties to cure for sufficient time and pay special attention to the state of the leak. Use a barcol hardness analyzer to attest that the cured putty has gained no less than 85 Shore D hardness.
Composite Pipe Wrapping
Utilize the latex gloves and open the Wrap Seal PLUS fiberglass repair tape followed by submerge it in water for 10 seconds, while smashing. Take off the fiberglass tape from the water and start wrapping the Wrap Seal PLUSTM fiberglass repair tape. The wrapping of fiberglass tape should start no under 100mm to 200mm before the leak locale. Wrap the pipe as hard and even-handedly as could be, pulling bit by bit after each round of wrapping. Utilize the entire roll over the pipe surface with no lesser than 50% cover for the entire pipe repair length. All length of wrapping should be in consent to the Engineering Calculation Report. Rehash the wrapping with a specific number of layers of Wrap Seal Plus fiberglass repair tape and finally decrease the lenght to around 25mm over every wrapping layer. The wrapping should be done in one bearing.
Examination of Repair
License the repaired zone to be cured for a couple of hours (period of time is dependent on pipeline working condition). Dissect to attest the last Barcol hardness estimation.
Repair work is done and the repaired structure can be worked back to normal working condition.